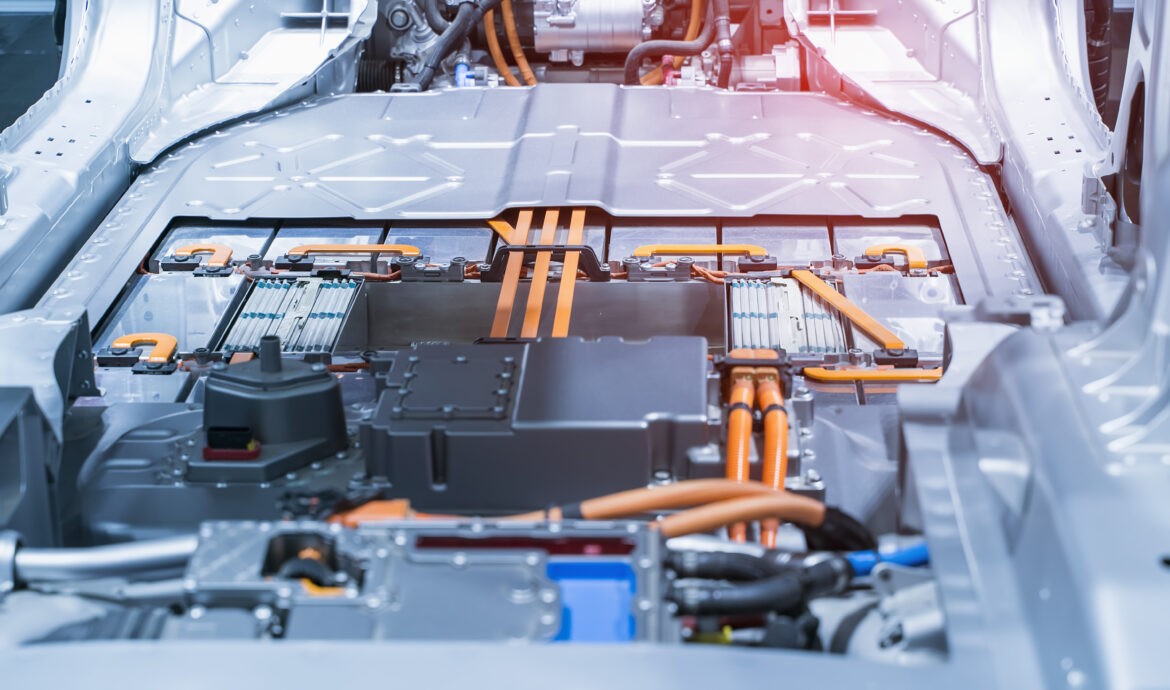
Why electric vehicles are more sustainable than you might think
On 12.01.2021 by Martin BeuseMartin Beuse recently defended his PhD in Battery Engineering & Public Policy at ETH. Martin is a mechanical engineer by training and has worked on battery and distributed energy topics as a strategy consultant before starting his PhD.
Despite the recent flood of (non-academic) studies claiming differently, battery-powered electric vehicles (BEV) already provide significant environmental benefits over internal combustion engine (ICE) cars. This gap is only widening, as policy, academia, and industry are coming together to rapidly improve BEVs and battery technology in particular.
Recently, many media reports have called the sustainability of battery-powered electric vehicles (BEVs) into question. As pointed out in an earlier Energy Blog post by Gracia Brückmann, this negative reporting is already affecting people’s purchasing decisions. This situation is particularly unfortunate as the science is clear on the environmental benefits of BEVs in comparison with internal-combustion-engine (ICE) cars. Furthermore, BEVs provide a clear pathway to true zero-emissions driving.
Does this mean that there is nothing that needs to be improved? Of course not! BEVs are far from being zero-emission vehicles and there are other environmental, social, and integrity risks along the battery value chain that urgently need addressing.
So where do we actually stand today and where are we going from here?
Challenges for Life Cycle Assessment (LCA) analyses: fast-improving and secretive industries
First, we need to address how we can actually measure and assess the status quo: LCA analysis assesses all environmental impacts of a technology along its full lifecycle, from cradle to grave. The great thing about LCA is that it is comprehensive, enables the identification of critical elements in the technology’s lifecycle, and the procedure for conducting one is standardized. Nevertheless, conducting LCA analyses for BEVs is particularly challenging for two key reasons:
- 10 years ago, there were virtually no BEVs on the road, but by the end of 2019 this went up to a stock of 4.8mn BEVs globally. Supply chains have been scaled up and production processes have become more efficient. Yet, naturally, LCA analyses can only be conducted ex-post, inherently looking into the past. For a technology where only marginal improvements are made every year, such as ICE vehicles, this is not a big problem. However, for BEVs, the differences can be stark. Famously, the IVL Swedish Environmental Research Institute in cooperation with the Swedish Energy Agency recently updated their study on emissions related to battery production. The new study, published in 2019, estimates battery emissions to be between 61 and 101 kgCO2e per kWh battery capacity, compared to 150 to 200 kgCO2e per kWh published just two years earlier!
- The battery industry is notoriously secretive when it comes to the specific materials they use and exactly how batteries are being produced. Even reverse-engineering batteries does not always provide a full picture. For example, finding cobalt in the battery does not tell you where and under which conditions it has been extracted, how it has been further refined, how it has been produced into the cathode material, and subsequently into the battery cell and pack.
The dynamics illustrated in point 1 give reason for optimism about BEVs’ environmental impacts, which are likely even lower than the latest scientific studies say. Regarding point 2, the draft for the new battery directive by the European Commission suggests to make carbon footprint declarations for BEV batteries mandatory. The so-called “battery passport” would also ensure materials and their origins are traceable.
In general, I would suggest thinking about these issues from the end goal rather than comparing technologies based only on a specific point in time. Which technology pathways allow us to go where we need to go, which is zero-emissions? How quickly can we get there and what needs to be done to get there?
Innovation will ensure further improvements in two key areas of current concern
CO2 footprint over a vehicle’s lifetime:
State of the art: The science is clear: BEVs already emit much less CO2e over their lifetime than comparable ICE vehicles. Auke Hoekstra summarized five common pitfalls of non-scientific studies in his recent paper.
- Emissions from battery production are often overstated. Outdated data is one key reason (see example of IVL study above).
- Not only have emissions from producing batteries been reduced, battery lifetimes have also been increased. Reducing the need for battery replacements improves the carbon footprint over the lifetime of the BEV.
- While economies worldwide are decarbonizing their electricity systems, these improvements are often overlooked when computing the emissions from BEV charging.
- Emissions associated with fuel production for ICE vehicles are not accounted for.
- Fuel economy of ICE vehicles is overestimated, not taking into account real-world driving behaviors (think: “diesel gate”).
Innovation perspective: Many further levers for improvement are already being tackled by the industry. A recent study by the World Economic Forum quantifies seven key levers to improve the carbon footprint of BEVs by 2030. Highest emissions reductions are expected from improvements to battery technology (especially the trend to higher energy densities), shared mobility, and using renewable electricity to charge the BEV. Furthermore, battery utilization may be increased (more kWh output per CO2e input) by vehicle-to-grid (providing services to the electricity grid with the BEV battery), repurposing the battery for a second-life after its retirement from the BEV, and improved recycling processes. Future batteries and electric vehicles can be designed with “circularity” built-in from the start, allowing for easier repairs, repurposing, and recycling.
Additionally, production processes can be further improved by avoiding the most energy-intensive steps. For example, one of the most energy-intensive production steps is the drying of the wet electrode slurries. Tesla recently announced that they are about to commercialize a so-called dry-coating process, which consequently does not require any energy for drying. Another consideration is the global supply chain structure: while most batteries are currently produced in China, where the energy mix is relatively carbon-intense, the European Union is leading a substantial effort to bring cell manufacturing and other production steps in the battery supply chain to Europe. Planned capacities already exceed 400GWhs.
Issues along the materials supply chain:
State of the art: A common misconception about the materials needed for BEVs, and the batteries therein, is that a lot of rare earths are necessary. The key metals needed for today’s lithium-ion batteries are lithium, nickel, manganese, and cobalt. None of these are rare earths. Actually, lithium is rather abundant in the earth’s crust. For the foreseeable future, researchers don’t expect fundamental shortages in battery material reserves. That doesn’t mean that there might not be temporal supply and demand imbalances, as lead times to develop new mines can be quite long.
There are, however, other environmental and ethical issues related to some of the materials used. Cobalt in particular has grabbed newspaper headlines time and time again regarding concerns about the conditions in certain uncertified, so-called “artisanal” mines (which currently make up for about 20% of capacity). In some of these mines child labor issues have been reported.
Innovation perspective: Cobalt content in battery cells has been rapidly reduced in recent years to increase energy density. The initial cathode material NMC111 (equal parts nickel, manganese, and cobalt) has been replaced by the market standard NMC622 (60% nickel, 20% each for manganese and cobalt) and NMC811 (you get it) is entering production now. Furthermore, improvements in vehicle efficiency and pack or cell design have allowed use of lower energy density cathode materials in some passenger cars (e.g., BYD’s “blade battery”, Tesla Model 3 produced in China). SVolt announced another “cobalt-free” battery chemistry last year.
Yet, the reality is also that at least until 2030, all major forecasters still expect significant amounts of cobalt to be necessary in global battery production. Therefore, multiple initiatives (both public and private) have been launched to improve the conditions in cobalt mines and to improve sourcing practices to ensure ethical cobalt mining. Similar initiatives need to be pushed forward for other key materials, as well. I think it is great that people are working on solutions and we should also start putting the same scrutiny to not just BEVs but other products we all use.
In sum, BEVs are the way to go for decarbonization of personal transport. They are always better than the alternative and provide a clear pathway to zero emissions. Yet, there is still more work to be done to improve sustainability. Innovation is often underestimated, but policy, academia, and industry are on it!
Cover photo by © [xiaoliangge] / Adobe Stock
Keep up with the Energy Blog @ ETH Zurich on Twitter @eth_energy_blog.
Suggested citation: Beuse, Martin. “Why electric vehicles are more sustainable than you might think”, Energy Blog @ ETH Zurich, ETH Zurich, January 12, 2021, https://blogt.ethz.ch/energy/electric-vehicle-sustainability/
If you are part of ETH Zurich, we invite you to contribute with your findings and your opinions to make this space a dynamic and relevant outlet for energy insights and debates. Find out how you can contribute and contact the editorial team here to pitch an article idea!