This article is part of a series produced in collaboration with the Diplomatic Courier for the ETH Zurich exhibition at the Annual Meeting of the World Economic Forum 2020.
This robot is making concrete more sustainable, and more beautiful
by Shane Richmond, 21 January 2020
A 3D-printing robot has been used to create a dance installation that could point to the future of concrete construction.
Students of architecture and digital fabrication at ETH Zurich wanted to know how emerging digital technologies could be used to create a contemporary take on the column typology - a key feature of architecture for thousands of years.
As well as serving the practical function of supporting the weight of a structure, columns have traditionally been decorated too, as a way of increasing a building's aesthetic appeal. In fact, so integral have columns been to the human environment that they are often used in non-structural ways, as monuments or purely decorative features.
Students of architecture and digital fabrication at ETH Zurich wanted to know how emerging digital technologies could be used to create a contemporary take on the column typology - a key feature of architecture for thousands of years.
As well as serving the practical function of supporting the weight of a structure, columns have traditionally been decorated too, as a way of increasing a building's aesthetic appeal. In fact, so integral have columns been to the human environment that they are often used in non-structural ways, as monuments or purely decorative features.
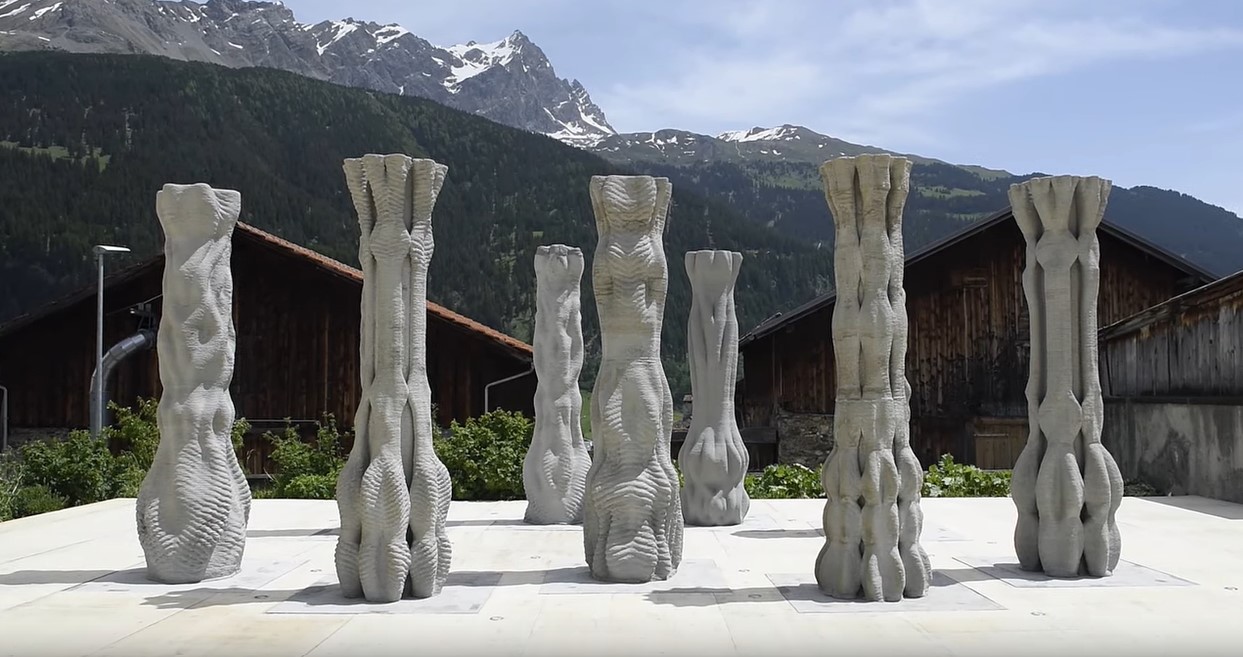
These concrete pillars are made by a 3D printing robot. Image from ETH Zurich.
Increasingly, those columns have been made from concrete, which is the most widely used substance on earth, after water. It's also a challenge for the environment because, by some estimates, concrete is responsible for as much as eight per cent of the world's CO2 and consumes a 10th of the world's industrial water. We are reliant on concrete and that will not change in the near future, but any technology that enables us to use less concrete will be hugely beneficial.
That's why students on ETH Zurich's Master of Advanced Studies in Digital Fabrication and Architecture program were keen to explore the possibilities that could be unlocked by new technology. The result was Concrete Choreography, an installation first seen at Riom, Switzerland, for the Origen Festival in the summer of 2019.
Layer by layer
The installation consists of nine columns, each 2.7 metres high, produced during a 10-week project. Transported by truck to the site in the Swiss alps, the pillars formed a stage and an interactive environment, in which dancers would perform. In December 2019, a new version of the installation was constructed for the World Economic Forum in Davos.
The pillars were constructed by a fully-automated, robot 3D printer that built them up, layer-by-layer, at a rate of 180 millimetres per second. Each one took two-and-a-half hours to print, in total, using a special fast-setting concrete mix.
This novel printing process was developed through interdisciplinary collaborations between Digital Building Technologies and Physical Chemistry of Building Materials, both research groups of ETH Zurich that are supported by the National Center of Competence in Research in Digital Fabrication.
The aesthetic potential of the new approach shows in the designs: each of the nine columns has its own fluid shape and surface texture. They were created using computational design, a process in which computers test possible approaches based on parameters set by human designers. This allows complex designs, such as those of each pillar, to be developed and tested far more quickly than otherwise, because computers handle much of the complexity.
The pillars were constructed by a fully-automated, robot 3D printer that built them up, layer-by-layer, at a rate of 180 millimetres per second. Each one took two-and-a-half hours to print, in total, using a special fast-setting concrete mix.
This novel printing process was developed through interdisciplinary collaborations between Digital Building Technologies and Physical Chemistry of Building Materials, both research groups of ETH Zurich that are supported by the National Center of Competence in Research in Digital Fabrication.
The aesthetic potential of the new approach shows in the designs: each of the nine columns has its own fluid shape and surface texture. They were created using computational design, a process in which computers test possible approaches based on parameters set by human designers. This allows complex designs, such as those of each pillar, to be developed and tested far more quickly than otherwise, because computers handle much of the complexity.
However, printing the final designs, including surface ornamentation, was no simple matter. In fact it was only achievable because the 3D printer can print in 'high resolution' - each concrete layer is just five millimetres thick and 25 millimetres wide.
But as well as the aesthetic possibilities, the new process has encouraging potential for a more sustainable way to build with concrete. The layering process means that the pillars can be hollow, so they use less material than traditional methods of construction. They also don't require any 'formwork' during the construction process.
Formwork is the mould, usually made from wood or steel, into which concrete is poured and held in shape while it sets. Usually these are temporary, though sometimes the formwork becomes part of the completed structure. Doing away with formwork also means using fewer materials, which adds to the sustainability of this method.
Though it is a showcase for the technology at the moment, this combination of age-old material and cutting-edge fabrication process shows the potential for rethinking how large-scale construction projects are handled.
Read more about this on the Diplomatic Courier.
But as well as the aesthetic possibilities, the new process has encouraging potential for a more sustainable way to build with concrete. The layering process means that the pillars can be hollow, so they use less material than traditional methods of construction. They also don't require any 'formwork' during the construction process.
Formwork is the mould, usually made from wood or steel, into which concrete is poured and held in shape while it sets. Usually these are temporary, though sometimes the formwork becomes part of the completed structure. Doing away with formwork also means using fewer materials, which adds to the sustainability of this method.
Though it is a showcase for the technology at the moment, this combination of age-old material and cutting-edge fabrication process shows the potential for rethinking how large-scale construction projects are handled.
Read more about this on the Diplomatic Courier.